Verschwendung reduzieren, Wertschöpfung maximieren
Durchlaufzeit – Was ist das?
Durchlaufzeit ist laut Gabler-Definition die „Zeitspanne, die bei der Produktion eines Gutes zwischen dem Beginn des ersten Arbeitsvorganges und dem Abschluss des letzten Arbeitsvorganges verstreicht.“ Unter Gut können Sie hier sowohl das physische Produkt als auch eine Dienstleistung verstehen.
Die Durchlaufzeit eines Auftrages wird weiterhin definiert als die „Summe der Bearbeitungs-, Transport- und Wartezeiten auf allen Produktionsstufen“. Das heißt, so lange sich der Auftrag auf irgendeine Weise in Ihrem Unternehmen befindet – als Bestellung auf dem Papier, als Halbfertigprodukt an der Maschine, als Fertigprodukt im Lager oder als Sendung auf dem Lastwagen –, erlebt Ihr Kunde dies als Wartezeit.
Oft überrascht es Führungskräfte, wie lange Güter oder Aufträge in ihrem System tatsächlich unterwegs sind. Besonders interessant ist bei genauerem Hinsehen die Entdeckung, wie die Produktion für das Produkt benötigt.
Denn die sogenannte Bearbeitungszeit, die lediglich Zeiträume einschließt, in denen das Produkt weiterverarbeitet wird, macht oft nur einen sehr geringen Prozentsatz der gesamten Zeit aus. Wenn es nur wenige Stunden dauert, ein ganzes Auto zu montieren (Bearbeitungszeit), warum müssen Käufer dann oft monatelang auf seine Lieferung warten (Durchlaufzeit)?
Der Grund dafür liegt oft in Wartezeiten, Transport, Wartung der Maschinen, Krankheit beim Personal, Fehlmengen bei den Vorprodukten und so weiter. Eine hohe Durchlaufzeit wird selten von Fehlern oder ungeplanten Unterbrechungen verursacht, sondern ist meistens im Prozessablauf eingeplant.
Selbst ein Unternehmen, das die meisten Waren im Lager führt, am Tag der Bestellung kommissioniert und versendet, wird eine relativ lange Durchlaufzeit im Verhältnis zur Bearbeitungszeit erleben. Denn auch wenn der Auftrag nur eine halbe Stunde lang von Ihnen bearbeitet wird, kommt er erst nach ungefähr 24 Stunden beim Kunden an. Den größten Teil seiner Zeit wartet er auf einem Lastwagen oder in einem Logistik-Hub.
Prozesse straffen, Zeit einsparen
Wie können Durchlaufzeiten reduziert werden?
Besonders die verschiedenen Werkzeuge von Lean Production, die dem japanischen Toyota Produktionssystem entstammen, haben die kürzere Durchlaufzeiten zum Ziel. Die Verkürzung des Aufenthalts eines Auftrages im System löst mehrere Probleme gleichzeitig: Sie erhöht die Kundenzufriedenheit durch kürzere Wartezeiten, verringert die Lagerbestände und damit die Kapitalbindung. Ausgangspunkt ist eine Analyse der zugrunde liegenden Prozesse. Das sind in erster Linie die direkt beteiligten Produktionsprozesse. Wichtig sind häufig auch bedeutende Hilfsprozesse wie die Beschaffung der Rohwaren oder die Wartung und Bereitstellung von IT-Ausstattung. Selbst die Personalabteilung kann eine Rolle spielen, wenn häufig Krankheit oder unflexible Arbeitszeiten die Ursache für hohe Durchlaufzeiten sind.
Bei einem schrittweisen Durchgang der einzelnen Abläufe werden Sie die Elemente entdecken, die viel Zeit kosten. Stellen Sie beispielsweise Halbfertigwaren in einem großen Batch her, dessen Produktion zwei Tage dauert, dann ist das erste hergestellte Gut vielleicht bereits nach wenigen Minuten fertig. Es muss aber das Ende seines Loses abwarten, damit man es weiter verarbeiten kann. Daher ist eines der Grundprinzipien von Lean der sogenannte One-Piece-Flow. Hier geht es darum, einzelne Stücke oder so kleine Batches wie möglich zu produzieren.
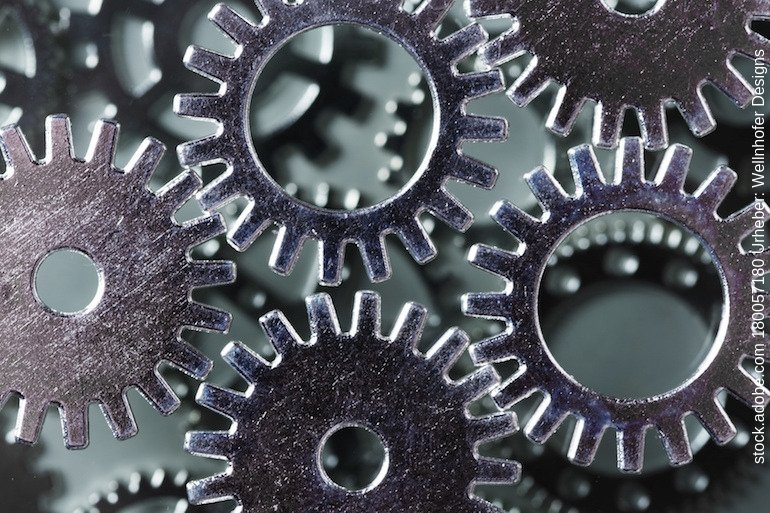
Auf diese Weise kann man mit minimaler Wartezeit den nächsten Schritt an diesem Gut ausgeführen werden. One-Piece-Flow ist daher eine sehr effektive Methode zur Verringerung der Durchlaufzeiten. Selbstverständlich gilt es dabei zu beachten, dass auch Rüstzeiten bei Bestimmung der optimalen Losgröße sehr wichtig sind.
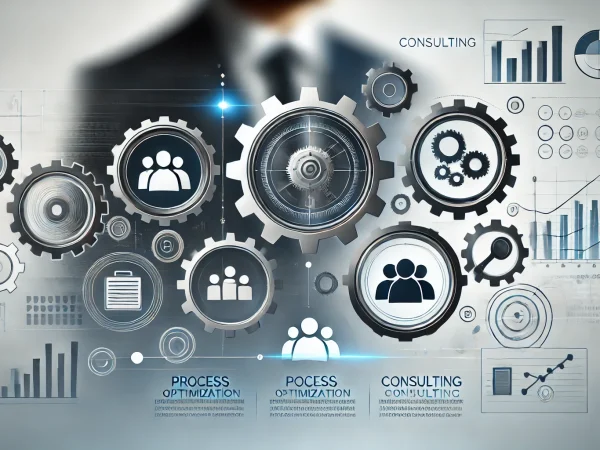
Ihr Partner für Prozessoptimierung
Optimieren Sie Ihre Prozesse mit unserer Expertise
Sichern Sie sich wertvolle Einblicke und Lösungen für Lean Management und Prozessverbesserung. Kontaktieren Sie uns für ein erstes individuelles Gespräch und erfahren Sie, wie wir Ihr Unternehmen effizienter machen können. Gemeinsam setzen wir Potenziale frei!
Effektive Strategien für schnellere Abläufe
Was sind die besten Methoden, um seine Durchlaufzeiten zu optimieren?
Die Verbesserung von Durchlaufzeiten kann auf verschiedenen Ebenen angegangen werden:
Im prozessorientierten Bereich:
Die Wertstromanalyse als Tool aus der Lean-Philosophie eignet sich hervorragend, um Prozesse zu analysieren. Sie nimmt Ausgangspunkt in dem Objekt, das das System durchfließt und deckt damit auch übergreifende Prozesse ab. Das heißt, die Wertstromanalyse schaut auch über die vier Wände der Werkshalle hinaus zu Lieferanten, dem Back-Office und den Kunden. Sie zielt darauf ab, den wertschöpfenden Anteil des gesamten Systems zu erhöhen. Das bedeutet gleichzeitig immer eine Reduzierung der Durchlaufzeit.
Aus einem organisatorischen Blickwinkel:
Traditionell sind Führungskräfte auf verschiedenen Ebenen für abgegrenzte Bereiche, Abteilungen oder Teams verantwortlich. Sie haben meist sowohl die Personal- als auch die Prozessverantwortung in einem definierten Teilbereich. Oft bedeutet diese Art der Organisation, dass die Verantwortlichen eifrig in ihrem Bereich optimieren. Übergange zu anderen Abteilungen und damit anderen Prozessschritten stehen weniger im Zentrum und sind oft suboptimal. Hierbei kann eine Organisation im Sinne eines Wertstrom-Managements helfen. Hier ist eine Führungskraft für einen Wertstrom von Anfang bis Ende zuständig und damit auch für die Durchlaufzeit. Der Verantwortliche kann hier an ganz verschiedenen Stellen der Prozesskette ansetzen, ohne das Verantwortungsgebiet eines Kollegen zu durchkreuzen.
Auf dem strategischen Niveau:
Die Positionierung von Lieferquellen, Produktion und Distribution kann für die Durchlaufzeiten von hoher Bedeutung sein. Verbringen Rohstoffe grundsätzlich sechs Wochen auf einem Containerschiff, bevor sie der Fertigung zur Verfügung stehen, bedeutet das in der Regel hohe Lagerbestände und geringe Flexibilität in der Fertigung. Auch die geografische Lage von Produktion und Distribution in Bezug auf die Abnehmer und die Länge der Transportwege zwischen ihnen sind ausschlaggebend für die Zeit der Aufträge im Gesamtsystem.
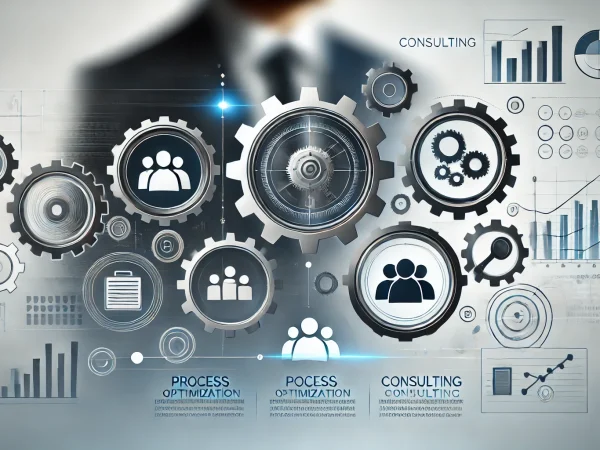
Ihr Partner für Prozessoptimierung
Optimieren Sie Ihre Prozesse mit unserer Expertise
Sichern Sie sich wertvolle Einblicke und Lösungen für Lean Management und Prozessverbesserung. Kontaktieren Sie uns für ein erstes individuelles Gespräch und erfahren Sie, wie wir Ihr Unternehmen effizienter machen können. Gemeinsam setzen wir Potenziale frei!
Was versteht man unter Durchlaufzeit in der Produktion?
Die Durchlaufzeit ist die Zeitspanne, die ein Produkt benötigt, um alle Produktionsschritte zu durchlaufen – vom Auftragseingang bis zur Auslieferung. Sie umfasst Bearbeitungszeit, Rüstzeit, Transportzeit und Wartezeit und ist ein wichtiger Indikator für die Effizienz der Prozesse.
Warum ist es wichtig, Durchlaufzeiten zu optimieren?
Die Optimierung der Durchlaufzeiten ist entscheidend, weil sie:
- Kosten reduziert: Weniger Stillstand und Verschwendung führen zu Einsparungen.
- Kundenzufriedenheit steigert: Schnellere Lieferzeiten verbessern die Kundenbindung.
- Liquidität erhöht: Kürzere Durchlaufzeiten beschleunigen den Cashflow.
- Flexibilität verbessert: Schnelle Reaktion auf Marktveränderungen wird möglich.
Welche Faktoren beeinflussen die Durchlaufzeit?
Die Durchlaufzeit wird beeinflusst durch:
- Wartezeiten: Stillstand aufgrund von Engpässen oder fehlendem Material.
- Rüstzeiten: Zeit, die benötigt wird, um Maschinen für einen neuen Auftrag einzurichten.
- Transportzeiten: Unnötige Wege innerhalb der Produktion.
- Prozessschritte: Zu viele oder ineffiziente Arbeitsschritte.
- Bestandsmengen: Hohe Lagerbestände verlängern die Durchlaufzeit.
Welche Methoden helfen, die Durchlaufzeit zu reduzieren?
Folgende Methoden sind besonders effektiv:
- Wertstromanalyse: Identifizierung und Eliminierung nicht-wertschöpfender Aktivitäten.
- Lean Management: Vermeidung von Verschwendung (z. B. unnötige Transporte oder Wartezeiten).
- Rüstzeitoptimierung (SMED): Verkürzen der Maschinenumrüstzeiten.
- One-Piece-Flow: Produkte einzeln statt in großen Losen fertigen.
- Automatisierung: Reduzierung manueller Prozesse zur Beschleunigung.
Welche Rolle spielt die Wertstromanalyse bei der Durchlaufzeitoptimierung?
Die Wertstromanalyse ist eine zentrale Methode, um die Durchlaufzeit zu optimieren. Sie visualisiert den gesamten Produktionsprozess und zeigt auf, wo Wartezeiten, Transportwege und überflüssige Prozessschritte liegen. Durch diese Transparenz können gezielt Maßnahmen zur Beseitigung von Engpässen und Verschwendung ergriffen werden.
Welche Vorteile ergeben sich aus der Optimierung der Durchlaufzeiten?
Die Optimierung der Durchlaufzeiten bietet zahlreiche Vorteile:
- Schnellere Lieferzeiten: Kundenaufträge werden zügiger erfüllt.
- Kostensenkung: Reduzierte Warte- und Lagerzeiten sparen Geld.
- Höhere Produktivität: Effizientere Abläufe führen zu mehr Output.
- Flexibilität: Bessere Anpassung an Kundenwünsche oder Marktveränderungen.
- Wettbewerbsvorteil: Schnellere Reaktionszeiten stärken die Position im Markt.