Rüstzeiten optimieren ist immer dann notwendig, wenn unterschiedliche Produkte mit den vorhandenen Maschinen hergestellt werden sollen. Dafür muss die Produktion umgestellt und die Werkzeuge getauscht werden. Immer, wenn das passiert, vergeht Zeit und die kostet Geld. Aus diesem Grund versuchen viele Unternehmen Umstellungen zu vermeiden. Damit tappen sie jedoch in eine andere Kostenfalle. Wir sagen Ihnen welche das ist und worauf es bei den Rüstzeiten wirklich ankommt.
Zeit optimieren, Produktivität steigern
Warum Rüstzeiten optimieren so wichtig sind
Wenn ein Betrieb seine Produktion umstellen muss, dann entstehen dabei Kosten. Neben Maschinenstillstandskosten fallen vergütungspflichtige Arbeitszeit an. Jede benötigte Minute wird dem Arbeitnehmer bezahlt. Das war früher schon anders. Aber heute ist da das Arbeitsrecht ganz eindeutig.
Aus diesem Grund versuchen Unternehmen in der Regel derartigen Aufwand zu vermeiden. Häufig probieren sie es mit der Steigerung der Losgrößen. Hierbei entsteht jedoch ein neues Problem. Was man an Arbeitszeit einspart, verliert man entsprechend durch die Steigerung der Kapitalkosten.
Denn: wird mehr produziert als ein Auftrag erfordert, dann füllt sich das Lager. Vorräte wiederum verlängern die Aktivseite der Bilanz. Diese müssen auf der Passivseite mit einer Finanzierung ausgeglichen werden. Dafür benötigt man zusätzliches Eigen- oder Fremdkapial. Durch den Lageraufbau wird also unnötig Geld gebunden. Zudem steigen die Aufwendungen für die Finanzierung – die Zinszahlungen. Vielen Unternehmern ist diese Kehrseite nicht bewusst. Sie verschenken dadurch Potenzial zur Verbesserung ihrer Wirtschafltichkeit. Dieses Thema sollte vermehrt Beachtung finden.
Die optimale Lösung bedeutet demnach eine Gesamtkostenrechung durchzuführen, um daraus zu sehen wie groß die optimale Losgröße ist. Neben der optimalen Losgroße sollten kürzere Rüstzeiten das Ziel sein. Damit die Mitarbeiter ihre Arbeitszeit effektiver nutzen können – um ihrer eigentlichen Arbeit nachgehen zu können. Der Weg dahin ist: eine Optimierung der Abläufe.
Stillstand minimieren, Effizienz maximieren
Was sind überhaupt Rüstzeiten?
Kurz etwas mehr zur Definition des Begriffs „Rüstzeit“:
Rüstzeit ist die die Zeit, die vergeht, während die Ausrüstung oder die Betriebsmittel einer Firma umgestellt werden. Diese Tätigkeiten sind erforderlich, um von der Herstellung eines Produktes zu der eines anderen zu wechseln. Rüstzeiten tragen nicht zur Wertschöpfung bei. Sie gelten als Verschwendung.
Typische Arbeiten beim Umrüsten sind:
- Vorbereitung
- Entfernen
- Montieren
- Justieren
- Testen und Anpassen
Vorbereitung
Alle Produkte des letzten Fertigungsloses werden entfernt. Der Abschluss des Auftrages kann im SCM-System am PC oder Rechner erfasst werden.
Dann wird der neue Auftrag angemeldet. Die benötigten Materialien werden vom Lager zur Verfügung gestellt.
Entfernen
Die Werkzeuge des vorherigen Produktes werden aus den Maschinen entfernt.
Montieren
Die Werkzeuge werden umgestellt auf die Erfordernisse des neuen Produktes.
Justieren
Testen und Anpassen
Der komplette Fertigungsprozess wird durchgeführt. Erste Test-Produkte werden gefertigt.
Sollten Probleme auftreten, die Arbeitszeit verschwenden, werden sie beseitigt. Jede Sekunde zählt. Denn die Summe der Einsparungen bestimmt den Erfolg des Unternehmens.
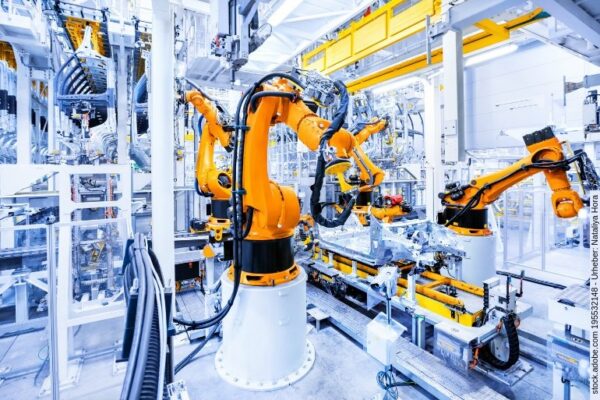
Prozesse analysieren, Wechselzeiten reduzieren
Wie können Sie Rüstzeiten optimieren?
In der Praxis hat sich die sogenannte SMED-Methode als Standard für die Optimierung der Abläufe ergeben. SMED-bedeutet:
Single Minute Exchance of Die
Übersetzt heißt es: Werkzeugwechsel im einstelligen Minutenbereich. Diese Methode ist darauf ausgelegt, die Rüstzeiten auf unter 10 Minuten zu reduzieren. Entwickelt wurde es Shigeo Shingō aus Japan. Er war wesentlich an der Entwicklung des hoch effizienten Toyota Produktionssystems beteiligt.
Bei der SMED-Methode werden die Rüstzeiten auf zwei Wegen reduziert:
- Organisatorische Maßnahmen
- Technische Maßnahmen
Ziel von SMED ist es, die Zeit zu reduzieren, in der die Produktion still steht. Dazu werden alle Abläufe so umgestaltet, dass eine Umrüstung der Produktion möglichst schnell erfolgt. Hier einige Beispiele, wie das erreicht werden kann:
Einige Aufgaben können parallel erledigt werden – während noch die Herstellung des alten Produktes läuft. Die Fertigungsmaterialien könnten bereitgelegt werden. Vorbereitende Arbeitsschritte können ausgeführt werden, wenn sie die laufende Produktion nicht stören. Beispielsweise das Waschen oder Vor-Reinigen von Rohstoffen. Oder, das Vorheizen einer technischen Apparatur.
Alle Abläufe werden standardisiert. Jeder einzelne Schritt wird im Plan festgeschrieben. Der Arbeitgeber muss ihre kontinuierliche Verbesserung sicherstellen. Dazu kann man sich im Betrieb regelmäßig gemeinsam zusammensetzen. Je nach Bedarf: täglich, wöchentlich oder auch monatlich.
Technische Geräte werden vereinfacht und ebenfalls standardisiert. Man verwendet idealerweise so oft wie möglich gleiche Komponenten. Beispiel: Wenn immer wieder dieselbe Schraubengröße verwendet wird, dann braucht man nur einen Schraubendreher und muss diesen nicht ständig wechseln. Auch das spart Zeit.
Das Arbeitssystem wird nach Fertigstellung einer Order in den ursprünglichen Zustand versetzt.
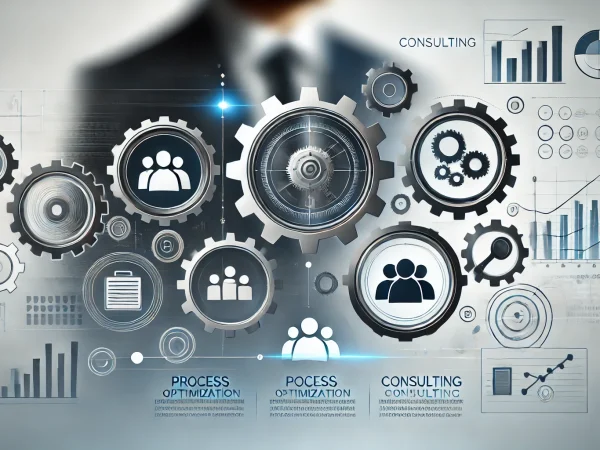
Ihr Partner für Prozessoptimierung
Optimieren Sie Ihre Prozesse mit unserer Expertise
Sichern Sie sich wertvolle Einblicke und Lösungen für Lean Management und Prozessverbesserung. Kontaktieren Sie uns für ein erstes individuelles Gespräch und erfahren Sie, wie wir Ihr Unternehmen effizienter machen können. Gemeinsam setzen wir Potenziale frei!
Praktische Tipps für schnelle Erfolge
Die besten Tipps auf einen Blick
Was versteht man unter Rüstzeiten in der Produktion?
Rüstzeiten sind die Zeiten, die benötigt werden, um Maschinen oder Anlagen für einen neuen Produktionsprozess vorzubereiten. Dazu gehören Tätigkeiten wie das Wechseln von Werkzeugen, das Anpassen von Maschinenparametern oder das Einrichten von Materialien. Sie verursachen Stillstand und können die Effizienz der Produktion stark beeinträchtigen.
Warum ist die Optimierung der Rüstzeiten so wichtig?
Die Optimierung der Rüstzeiten ist entscheidend, weil:
- Stillstand reduziert wird: Maschinen sind schneller einsatzbereit.
- Produktivität gesteigert wird: Mehr Zeit für die eigentliche Produktion.
- Kosten gesenkt werden: Weniger Zeitverschwendung spart Ressourcen.
- Flexibilität erhöht wird: Schnellere Umstellung auf neue Produkte oder Varianten.
- Kleinere Losgrößen möglich werden: Unternehmen können kundenindividueller produzieren.
Welche Methoden gibt es zur Optimierung von Rüstzeiten?
Die bekannteste Methode zur Optimierung von Rüstzeiten ist SMED (Single Minute Exchange of Die). Sie umfasst:
- Analyse: Alle Rüstvorgänge dokumentieren und analysieren.
- Interne und externe Tätigkeiten trennen: Aufgaben während des Maschinenstillstands (intern) und Aufgaben, die parallel laufen können (extern).
- Externe Tätigkeiten optimieren: Vorbereitungsarbeiten außerhalb der Stillstandszeit erledigen.
- Interne Tätigkeiten vereinfachen: Werkzeuge standardisieren, Schnellwechselsysteme einsetzen.
- Standardisierung und Schulung: Rüstprozesse festlegen und Mitarbeiter schulen.
Welche Werkzeuge und Technologien unterstützen die Rüstzeitoptimierung?
Folgende Werkzeuge und Technologien können helfen:
- Schnellspann- und Schnellwechselsysteme: Ermöglichen einen schnellen Werkzeugwechsel.
- Checklisten und Standardabläufe: Reduzieren Fehler und beschleunigen den Prozess.
- Automatisierung: Einsatz von Robotern oder CNC-Programmen für Umrüstvorgänge.
- Digitale Werkzeuge: Software zur Planung und Überwachung von Rüstzeiten.
- SMED-Workshops: Praxisnahe Schulungen zur Analyse und Optimierung der Rüstprozesse.
Was sind häufige Hindernisse bei der Optimierung der Rüstzeiten?
Typische Hindernisse sind:
- Fehlende Analyse: Ohne klare Datengrundlage bleiben Optimierungspotenziale ungenutzt.
- Widerstand der Mitarbeiter: Veränderungen werden oft als zusätzliche Belastung empfunden.
- Unzureichende Schulung: Mitarbeiter kennen die neuen Abläufe oder Werkzeuge nicht.
- Mangelnde Standardisierung: Unterschiedliche Prozesse führen zu Ineffizienz.
- Fehlende Investitionen: Notwendige Technologien wie Schnellwechselsysteme werden nicht angeschafft.
Welche Vorteile bringt eine erfolgreiche Rüstzeitoptimierung?
Eine optimierte Rüstzeit bringt folgende Vorteile:
- Höhere Maschinenverfügbarkeit: Mehr Zeit für produktive Tätigkeiten.
- Kostenreduktion: Weniger Stillstand führt zu geringeren Produktionskosten.
- Steigerung der Flexibilität: Schnelle Umstellung auf neue Produkte oder Varianten.
- Produktivitätssteigerung: Bessere Auslastung der Maschinen und Mitarbeiter.
- Wettbewerbsvorteile: Unternehmen können schneller und kostengünstiger auf Kundenanforderungen reagieren.